Kanban stands for Kan- card, Ban- signal. The essence of the Kanban concept is that a supplier, the warehouse or the manufacturer should deliver components only when they are needed so that there is no excess inventory. Within this system, workstations located along production lines only produce or deliver desired components when they receive a card and an empty container, which indicates that more parts are needed in production.
In case of line interruptions, measures are taken so that each workstation will only produce enough components to fill the container and then stop. Kanban also limits the amount of inventory in the process by acting as an authorization to produce more. Since Kanban is a chain process in which orders flow from one process to another, the production or delivery of components is pulled through the production line. This is in contrast to the traditional make-to-forecast and make-to-order methods where parts are ‘pushed’.
In JIT systems, when components and parts are needed for final assembly, they are pulled in small batches from the supplying work centers. One of the most popular methods used for implementing JIT is through the use of Kanbans.
On-Screen Dispatching
GLOVIA G2’s Kanban inventory control system provides on-screen dispatching of inquiries and reports that provide factory supervisors with the information they need to control the production floor. This up-to-the-minute input provides a powerful tool for monitoring currently scheduled operations, work center loading and priority sequencing. It also provides the visibility into what needs to be completed in order to ensure a smooth and coordinated production flow.
Advantages of Kanban Processing in the Inventory Control System
- Provides quick and precise information
- Provides quick response to changes
- Avoids overproduction
- Minimizes waste
- Maintains full control
- Delegates responsibility to line workers
Kanban Processing in GLOVIA G2
As part of our ongoing commitment to provide the best manufacturing management practices within GLOVIA G2 ERP software, we have introduced a system that encompasses the very best of Kanban techniques. To help create as much flow as possible, monthly requirements are calculated using GLOVIA G2 Master Production Scheduling, which then relays information to a Kanban screen and generates the required number of Kanbans.
Referring to the above diagram, when a shipment is due, the Kanban inventory control software module generates pack lists and container labels. For each label that is created, a warehouse staff individual must select a full container to go with each corresponding container label (C). In order to replenish the finished goods storage, a production Kanban is selected and scanned to match the outgoing container that is already full. After the operator compares and confirms a match, the production Kanban is then sent to the production line, on a Heijunka post (where the Kanbans reside) as an authorization to produce another container of parts. When the production line has finished producing a full container of parts, the production Kanban is finally placed in the matching container and moved to finished goods storage (B). If preferred, the production line can also be updated by using a move Kanban to move stock through the production line and to component storage (A).
To keep data entry to a minimum, all Kanbans are produced with bar codes and the system is ready to accept data entry through scanners or other means.
Download the CrescentOne data sheet to learn more about how GLOVIA G2’s Kanban inventory control system can improve manufacturing efficiency.
DownloadExplore More Capabilities
Select a product category below to see how CrescentOne can improve a particular aspect of your business
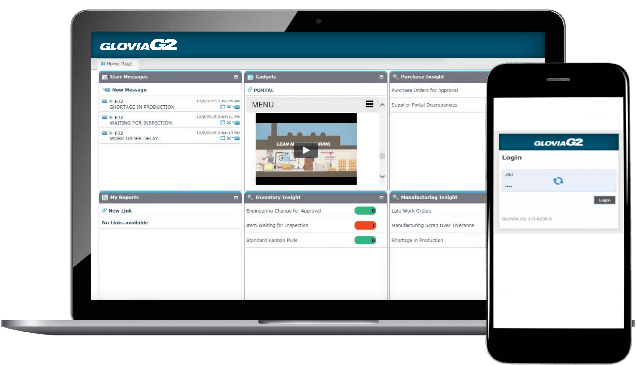