GLOVIA G2 Quality Management ensures you maximize the effectiveness of your quality team so that they ensure you exceed your quality goals. The solution drives balanced, methodical, measured, quality processes that yield consistent, dependable results. The ability to immediately view and upload procedures, photographs, drawings, instructions, measurements, non-conformance reports, etc. directly from their GLOVIA G2 transactions maximizes visibility and the time your whole team has to spend on activity that is productively adding value.
GLOVIA G2 drives Consistent Quality
Industry standard methodologies are embedded in the solution:
‘First Article Inspection’
‘Lot skip’
‘Acceptable Quality Limits (AQL)’ – AQL represents the fundamental foundation of the majority of Global Quality standards (i.e. MIL STD 105E, ANSI/ASQ Z1. 4, ISO 2859).
Embedding these capabilities into a single integrated solution is the only way to automate many of the mundane repetitive decision making processes that your quality team has to perform. Relieving them of these tasks allows them to maximize their effectiveness and provide the following business benefits:
Inventory can be ‘put away’ immediately without having to involve inspectors and with minimal delay to physical availability. This is possible because GLOVIA G2 Uses ‘Lot Skip’ policies to automatically determine and advise the user whether inspection can be skipped or not during the receipt/completion transactions.
Your quality team can focus on assessing quality instead of losing time using charts or switching software to figure out what inspection activity needs to be conducted, evaluating the results, and, assessing the impact on future inspection activities. This is possible because GLOVIA G2 automatically identifies what sampling is needed, what procedures are to be followed, what measurements/results are to be recorded, what constitutes acceptable quality, and, whether future inspection activities need to be tightened or relaxed.
A Stitch in time!
Stop wasting time and money adding value to material that is already non-conforming!
Conducting ‘Line-side’ inspections as part of the production process typically results in significant benefits in terms of both quality and cost control. However, ‘Line-side’ inspections can be very difficult to implement without real-time visibility of production and inspection schedules/resources. GLOVIA G2 ‘Dispatch lists’ provide your production and quality control teams with both the visibility and swift update capabilities they need to ensure:
Inspectors know exactly where to go and when,
Both Production and inspection activity is promptly and accurately recorded in real-time,
WIP value and down-time attributed to ‘items waiting inspection’ is minimal,
Non-conformances can be identified earlier before further wasteful production activity is conducted and unnecessary cost incurred, and,
The real cost of scrap and re-work is accurately measured.
Failure Alerts extend that real-time visibility by providing immediate notifications of quality issues both inside and outside the organization. Failure Alerts can be used to immediately notify other quality team members, supervisors, executives, buyers, supplier contacts, etc. This maximizes the time available to rectify the situation and minimizes any impact.
Disposition and Resolution Management
The Inventory of materials that initially appear to be defective/non-conformant is segregated awaiting Material Review. Once reviewed, Dispositioning and resolution management capabilities provide for the visibility, segregation and control of those materials it is deemed require to be re-worked, returned to the supplier or scrapped.
Suppliers, Customers and Quality
The ability to effectively manage and resolve Customer and Supplier quality issues is paramount. Below are some of the key features available:
Customer Returns authorization and processing,
Warranty and Extended Warranty management,
Lot/Serial Traceability,
Supplier Returns management,
Automatic generation of credit memos for defective materials,
Supplier Payment withholding until required certification/documentation is received,
Supplier Performance Analysis and rating in support of score-carding,
Quality Control management that can be generic or specific to a supplier, item and order where needed.
Failure Alerts immediately notify buyers and supplier contacts of quality issues.
Focused Quality – Integrated and Business-Wide
The data collected in Quality Management can be used to provide visual analytical insights that can drive quality initiatives in all areas of your business from Product Definition, through Sales, and on to Financial Reporting.
The costs of in-process, assembly and component scrap along with re-work costs and returns – seamless flow through the integrated applications and are accurately reflected as actual costs in the various engineering, purchasing, manufacturing, inventory, costing and financial applications.
Whatever Quality Management and process improvement programs your company chooses to implement, whether it’s Six-Sigma, Kaizen, Total Quality Management (TQM), or process standardization required to meet ISO requirements; GLOVIA G2 can provide the information you need.
Download the CrescentOne for more information about the GLOVIA G2 Quality Management ERP Module for manufacturing.
DownloadExplore More Capabilities
Select a product category below to see how CrescentOne can improve a particular aspect of your business
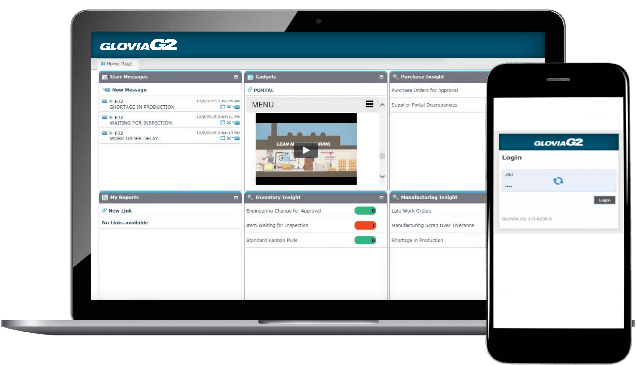